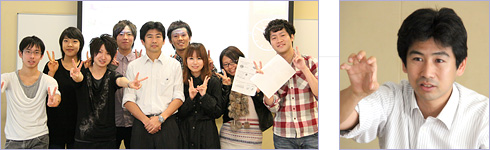
Internationalization of Japanese Kaizen Activities
Kaizen activity is a term generally and broadly used in Japanese manufacturing industries to refer to activity that is implemented onsite by recognizing and bridging the gap between ideal and actual conditions and applying ideas to improve a production situation. Growth in overseas direct investments from 1980 onwards gave Japanese companies the momentum to actively develop kaizen activities by transferring their business operations to local subsidiaries abroad. Complementing this trend, such people as Taiichi Ohno (1978), who had initially developed the Toyota Production System, Schonberger (1982) and Womack et al. (1990) introduced the subject of how widely effective kaizen activities were throughout Japan and the world. The concept of “kaizen” is now used globally in manufacturing industries as a matter of course, and kanban (information card), andon (problem display board) and poka-yoke (error prevention) methods are used in many companies overseas besides Japanese subsidiaries. Nonetheless, it has been said that not many of these companies overseas have firmly implemented kaizen activities at a practical level for everyday onsite application. To identify the reasons for this, a field survey of a total of 17 automobile and component plants in Japan, the U.K. and Germany was conducted. The following results of this survey can give us insight into kaizen activities in those locations.German Kaizen Activities
German kaizen activities have a strong tendency to be promoted under the leadership of managers and to be specialist-oriented. A relatively clear system for the division of labor is in place among different functional specialists in German kaizen activities. Unlike the case in Japan, manufacturing teams (operators in particular) in Germany do not have major opportunities to be involved with kaizen activities. Instead, meisters play central roles in onsite improvements. Since the position of a meister in Germany is similar to the position of a manager (rather than a manufacturing team leader) in Japan, it seems that a managerial level of understanding of a given workplace is considered to be essential for promoting kaizen activities in German plants.Japanese Kaizen Activities
Generally, kaizen activities in Japan are considered to be led by manufacturing teams, with the operators onsite having significant authority over those activities. However, the recent survey revealed that manufacturing managers and manufacturing team leaders actually have significant authority regarding most kaizen activities. The survey results hardly indicate that Japanese manufacturing operators possess specific authority and responsibility, although it is understood that as members of manufacturing teams, they have significant opportunities to be involved in kaizen activities. Japanese manufacturing teams have their own targets for improvement and conduct meetings to solve problems on a daily basis. In this regard, manufacturing team leaders play major roles as leaders in Japanese kaizen activities.British Kaizen Activities
Kaizen activities in British plants are similar to activities in Japan in many ways. Indeed, the plants targeted by the survey are deeply related to Japan, including overseas plants of Japanese companies and joint ventures. However, many of these plants are managed by British managers, with Japanese resident officers in mere advisory roles. Rather than attempting to transfer Japanese ways of doing work, such British managers are devising their own original ways of executing duties tailored to local conditions. Additionally, prior to developing kaizen activities at the worksite level, many plants are also recognizing the need to provide manufacturing team leaders and operators with careful education and training in implementation methods.Future Issues of Japanese Companies
These research results verify that Japanese companies still predominate over overseas companies in terms of team-based kaizen activities. At the same time, it was observed that teamwork at Japanese plants could become weaker for various reasons, such as increasing numbers of temporary workers and weakening of on-the-job-training. In this respect, Japanese companies face a challenging phase in which they should reconfirm the element of teamwork, which had been their strong point until now, and take serious approaches to revise their structures in order to be effective in international society in the future.Profile
Associate Professor of the School of Business Administration specialized in business administration theory.Born in 1970 in Saitama prefecture. Graduated from the School of Business Administration, Meiji University in 1993. Completed the master’s course of business administration in the Graduate School of Business Administration, Meiji University (MBA) in 1995. Completed the doctoral course in the Graduate School of Business Administration, Meiji University (PhD) in 1999. Full-time lecturer in the Department of Business Administration, Faculty of Economics, Kanto Gakuin University in 1999. Assistant Professor in the Department of Business Administration, Faculty of Economics, Kanto Gakuin University in 2002. Visiting Scholar, Judge Business School, University of Cambridge in 2006. Visiting Scholar, Cardiff Business School, Cardiff University in 2007. Became Associate Professor in the School of Business Administration, Meiji University in 2011.
Main Publications
Post-modern Organizational Theory: Dobunkan 2005 (in collaboration with Iwauchi, Takahashi and Murata)“Did the Nissan Revival Plan lead to the break-up of the keiretsu system?”: International Journal of Automotive Technology and Management, 2008, Vol.8, No.3 pp.297-316.
“Transferring Japanese kaizen activities to overseas plants in China”: International Journal of Operations & Production Management, 2008, Vol.28, Issue 6, pp.518-539. (Awarded 2009 Outstanding Paper Prize)
Academic Societies
Academy of ManagementAcademy of International Business
European Operations Management association